Salomon's Addikt Pro Ski Goes Big On Recycling
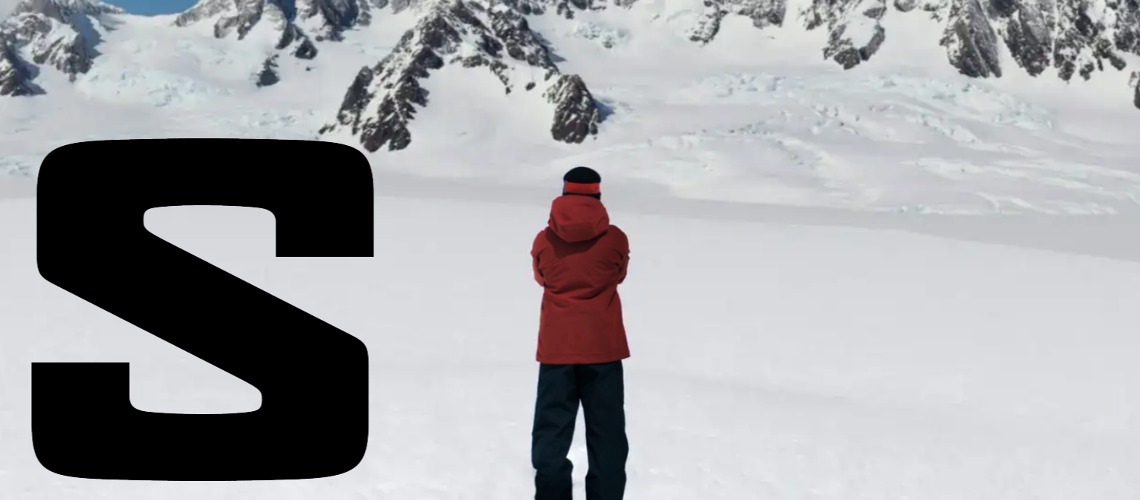
The new Salomon Addikt Pro on-piste carving ski uses technology from the company’s racing range to deliver the feeling of carving the perfect turn to more skiers. But that’s only part of the story. The ski also uses recycled materials in its sidewalls that comes in a variety of colors depending on the materials available at the time of production. How did Salomon’s R&D team make it happen? The waste material created by the ski production process was collected, recycled, and re-used in the sidewall construction of the skis.
First, let’s talk about the ski’s performance.
A Slalom-inspired ski with a radical racing design, the Addikt Pro incorporates Salomon’s iconic racing flag in its top sheet to subtly pay homage to the company’s rich racing history. The ski is engineered to combine high-performance technologies with the forgiveness qualities needed to make on-piste turns more, well, addictive.
Whether making sharp, short turns or arcing longer, faster turns with stability, the Addikt Pro is extremely agile and playful thanks to its 66mm slalom sidecut. From Salomon’s World Cup winning fleet of race skis, the Addikt Pro utilizes Salomon’s proven Blade technology, which fuses flexible polymer pads in the Titanium layer that make the ski easier to bend so skier’s enjoy powerful turns longer.
To add a layer of support to the ski, Salomon developed the Addikt exclusive Motion Tail technology, which increases tail flexibility by 5% to create a more forgiving yet responsive all-day ski.
"When we mill any ski sidewall, 40 to 50% of the material consumed goes to the trash. For the Addikt and Addikt Pro skis, this collected, re-fused and turned into a new sidewall. Performance characteristics remain un-changed and waste is reduced by almost half." said Arnaud De Mondenard Alpine Ski R&D Manager
USING RECYCLED MATERIALS IN THE SKI’S SIDEWALLS
Salomon’s Ski R&D team also found a way to reduce the Addikt Pro’s environmental impact by using fully recycled ABS sidewalls in the ski constriction. The design represents a completely new way for the company to processes factory ABS waste and uses it to build new 360° ABS sidewalls. What began as a test in Salomon ski prototype center at the company’s Annecy Design center two years ago, has been fully implemented in the factory and into Addikt range less than two years later.
“The sidewalls of the Addikt Pro and Addikt skis do not come from virgin, oil-based plastics, but from the material waste of our own production,” says Arnaud de Mondenard, Alpine Ski R&D Manager for Salomon. “When we mill any ski sidewall, 40 to 50% of the material consumed goes to the trash bin as chips. For the Addikt and Addikt Pro skis, these chips are collected, re-fused and turned into a new sidewall. Performance characteristics remain un-changed and waste is reduced by almost half.”
As a bonus, the sidewalls feature colorful patterns that add a noticeable flair to the look of the Addikt.
“Depending on the kind of skis produced before, Addikt sidewalls will show different random colors—varying from black to orange to yellow to green,” Arnaud says. “We’ll sometimes have various colors between two pairs, even within a pair, or in between the two sides of one ski.”
There were also improvements made on energy consumption during the Addikt ski manufacturing process after the team performed a life-cycle analysis on the MTN range of touring skis and implemented some changes.
“In the molding process of the Addikt Pro ski, we reduced the energy needed to press the ski by almost half compared to previous S/MAX ski models,” Arnaud explains. “The beauty of this company and this ski R&D team here in Annecy is we are able to test crazy things in our prototype center and then transform it to scale in our factories.”