Castle Mountain: Major Infrastructure Upgrades, In Excess Of $2M In Resort Improvements
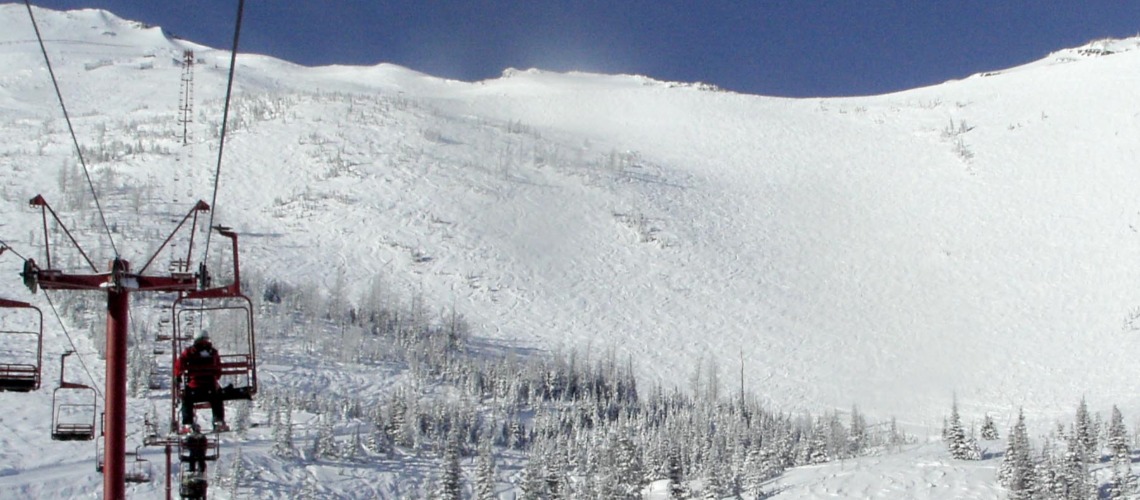
Following a Master Development Plan completed in 2017, Castle Mountain Resort is set to invest more than $2M in resort infrastructure projects that will be completed in advance of the 2019/2020 season. This summer’s projects include top to bottom snowmaking infrastructure in the Huckleberry terrain pod, on Whiskey Jack run, and within the base area in addition to the purchase of state-of-the-art snowmaking machines. A natural gas line, in partnership w/ ATCO, is currently being upgraded / installed and is poised to bring natural gas to the resort for the first time, starting this fall.
The additions will not only ensure more consistent snow conditions on the lower mountain & Huckleberry terrain but also opens up the possibility of pre-season training for various user groups (race clubs and/or ski academies), pushes Castle Mountain Resort’s planned opening day one week earlier (now set as December 7) and increases the possibility of remaining open later into April. As part of its agreement with ATCO, Castle Mountain Resort also absolves itself of prior propane gas distribution responsibilities, allowing it to focus more energy on exceptional ski resort operations.
“Over recent months we have closely examined the areas where we saw room for improvement at Castle Mountain Resort and looked for opportunities to create an even better experience for our residents and guests,” says Castle Mountain Resort general manager Brad Brush. “These infrastructure updates will have an immediate and dramatic impact for our visitors and we are excited to show off these changes starting this December.”
A key component of these updates is Castle Mountain Resort’s first water storage reservoir, representing a $375,000 expenditure which features a water intake in nearby Haig Creek. Designed to hold 6,700 cubic meters of water to assist in snowmaking efforts – an amount equivalent to three Olympic sized swimming pools – the reservoir will be connected to the snowmaking system as its primary water source. The resort has applied for and been issued a water license that will allow them to fill the reservoir only when water conservation objectives are met in the Castle River. Meltwater from machine-made snow will then return to the Castle River system come spring, additive free.
Snowmaking is getting a massive $1.4M investment. This includes the main pump house which is able to deliver 250 gallons per minute to Castle’s new network of waterlines, allowing four to six snow machines to run simultaneously. The pumphouse was designed with future snowmaking expansion in mind and the ability to add additional pumping capacity with subsequent implementation phases. New snowmaking infrastructure includes underground piping, electrical, hydrants, and power pedestals from the Huckleberry Reservoir to the top of Huckleberry Chairlift via Lone Ranger run, from Huckleberry Reservoir to the base area adjacent to the main day lodge via Round-up Traverse run, and from the base area adjacent to the main day lodge to the top of Whiskey Jack run.
Finally, Castle Mountain Resort, alongside local residents, has invested in a project which will see ATCO install new natural gas infrastructure from Beaver Mines to Castle Mountain Resort, including 7.5 kilometers of upgraded gas line and 16.7 kilometers of new gas line. ATCO’s takeover/conversion of Castle Mountain Resort’s existing propane distribution network will assist in lowering operational costs for the resort and lower utility costs for residents. Additionally, it will result in a reduction of 90 metric tons of green house gases / year roughly equated to taking 20 passenger vehicles off the road.