Perisher's Mt P 6 Takes Its First Passengers
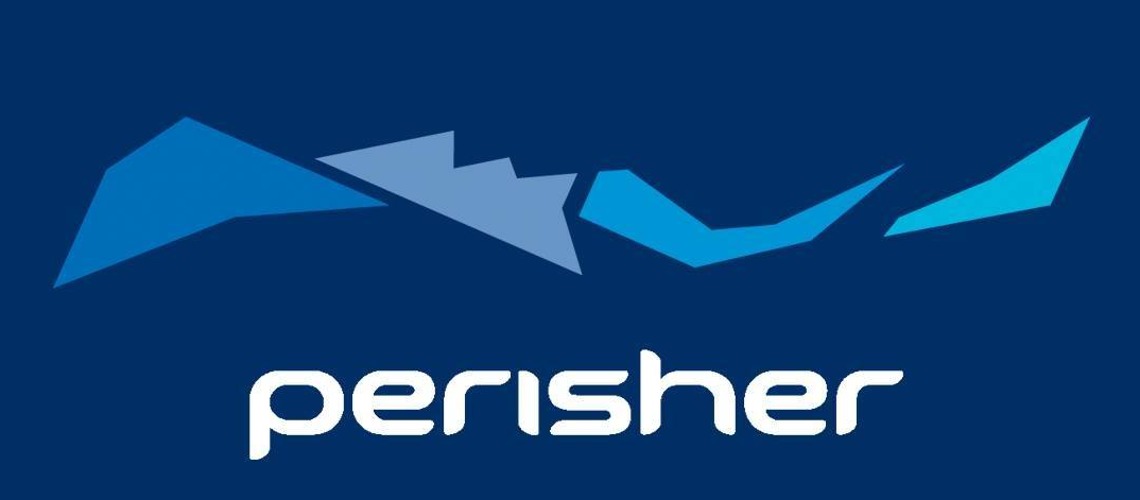
In an exciting milestone in the construction journey of their newest lift, the Mt Perisher 6 the chairlift carried its very first passengers!
While this wasn’t the official ‘first chair’ (a special milestone that is reserved for 6 lucky guests on the Mt P 6's first day of operations), it was an essential step in the lift’s commissioning process. The Mt P 6’s very first passengers were four members of the Perisher team who have been instrumental to the success of the project as well as two friends from Doppelmayr.
Together, they loaded onto the Mt P 6 for a carefully controlled test ride, marking a major milestone in ensuring the lift will spin this season.
What Goes Into Commissioning a New Chairlift?
- Building and opening a new chairlift is no small feat. The process begins long before the first chair spins, and it involves months of detailed planning, engineering, construction, and rigorous testing.
- After the physical structure is completed including towers, terminals, haul rope, and chairs, the lift enters the commissioning phase. This is where they check and double-check every system to ensure everything is functioning exactly as it should.
Commissioning involves:
- Mechanical testing – verifying the operation of the drive systems and safety controls
- Electrical testing – ensuring all sensors, controls, safety switches, and backup systems are functioning correctly
- Load testing – simulating the weight of passengers to confirm the lift can operate safely under full capacity
- Traditionally, ski resorts use water-filled containers (often garbage bins or drums) to simulate this passenger load. These are evenly distributed across the chairs to create the same kind of stress on the system that real guests would. It’s a safe and effective way to test lift capacity, but it only tells part of the story.
Why Testing With Real People Matters
- While water weights help test mechanical and structural performance, they can’t replicate the human experience. For the final stages of testing, they need real people to ride the lift.
This allows the team to:
- Observe the chair’s movement and timing from a guest’s perspective
- Test loading and unloading at full chair spacing
- Make sure all guest-facing elements (seat height, terminal speed, etc.) are working comfortably and efficiently
- Confirm the emergency procedures and lift operations are performing exactly as designed
It’s also an opportunity for our lift operations and maintenance teams to fine-tune the ride experience before guests ever set foot on the loading platform.