MDV Companies Volkl & Dalbello Say 'Yes We Care' About Sustainability
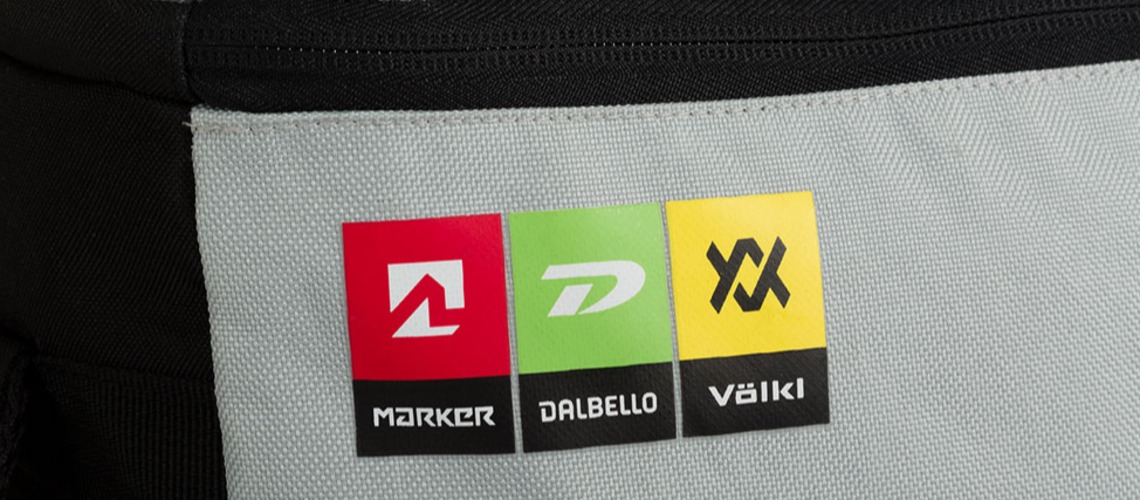
MDV companies Volkl and Dalbello are activiely pursuing a more sustainable approach to ski equipment production.
Dalbello is proud to be a partner of the LIFE RESKIBOOT project which targets the environmental problem of plastics waste management with a new model applied to ski boot construction.
LIFE RESKIBOOT will implement a new model of circular plastic economy over the full product life cycle, including take-back and re-use system from ski boot rentals for sorting and recycling of multi-plastics components in order to develop an optimized manufacturing process for ski boots.
LIFE RESKIBOOT will implement a new model of circular plastic economy, in line with the European Strategy for Plastics in a Circular Economy, over the full product life cycle, including a take-back and hard-outer shell re-use service for ski rentals, to manufacture ski boots from recycled soft and hard multi plastics.
The project objectives are:
- Launch on the market of ski boots made with about 90% of recycled raw materials (both for the construction of the external part and the internal part) obtained from post-consumer ski boots turned into secondary raw materials after a sorting method, based on electromagnetic effect, able to achieve a 95% separation efficiency for the polyurethane and foamed materials.
- Manufacture 1.000 pairs of ski boots, characterize and use them on real slopes to prove that they can be commercialized since perform well for skiers both in terms of comfort, technical features and safety properties.
- Develop an optimized manufacturing process for ski boots using about 90% recycled raw materials and eliminating processing offcuts that in current conventional processes are up to 40% of foamed materials used for the liner.
- Define a circular economy business model for ski rentals based on a take back system for post-consumers ski boots to be collected, sorted and turned into secondary raw materials.
- Define a new service for rentals to re-use the hard-outer shell and substitute the internal liner with a recycled one to overcome the actual 3-years rapid degradation of liners that imply that the whole ski boot is landfilled.
- Get an at least 7% reduction of ski boot final cost due to the combined effect of zeroing the manufacturing waste streams and the reduced use of virgin raw material.
- Measure the environmental and circularity performance of the new product system and show the improvement compared to the current baseline situation.
- Provide guidelines for market replication of ski boots that are designed to be more easily and efficiently separated, to be also applied to other types of sport footwear.
- Realize a certified environmental product declaration of the new ski boot and provide product category rules for other ski boots producers.
- At the end of the project 1.000 ski boot pairs for adults will be manufactured and tested by skiers to demonstrate comfort and technical performances.
Völkl's raw materials come from 100 percent European sources. For example, the wood used to make theirskis comes exclusively from European FSC- and PEFC-certified renewable sources. Their suppliers recycle 100 percent of the wood that cannot be used in ski production, for example to generate electricity. All the individual raw materials used in production in returnable wooden packaging without film wrapping that is reusable and sustainable.
They say:
As a ski manufacturer, protecting the global ecosystem is more important than ever for Völkl. Winter sports are disproportionately impacted by the growing burden on the environment and natural world, and depend on protecting the “white gold” found in the mountains. We at Völkl, the last remaining ski manufacturer in Germany, see protecting the environment as our responsibility, which is why sustainability and resource efficiency are so important to us. From the sourcing of raw materials and production to the use of our products and disposal – our efforts to be sustainable cover the entire life cycle of our products.
SOURCING AND PROCESSING OF RAW MATERIALS
Starting in the first stage in a ski’s life cycle – the sourcing and processing of raw materials – we put a premium on sustainability, relying on alliances with hand-chosen local partners. The raw materials we use come from 100% European sources. For example, the wood used to make our skis comes exclusively from European FSC- and PEFC-certified renewable sources. Our suppliers recycle 100% of the wood that cannot be used in ski production, for example to generate electricity, or by suppliers giving it directly to local farmers in the form of sawdust.
We transport the individual raw materials used in production in returnable wooden packaging without film wrapping that is reusable and sustainable. The location of the Völkl factory in Straubing, Germany, allows for short transport routes, reducing emissions of pollutants.
PRE-PRODUCTION OF PROTOTYPES
The “Made in Germany” quality promise means Völkl skis must meet high standards. Living up to them requires years of development, including extensive testing and optimisation of prototypes. The use of recycled and residual materials, along with misprinted surface materials, reduces waste in this stage of production. To keep prototype production to a minimum – and reduce our use of resources – we also often simulate the design of a new ski only using a computer. We assess our production processes annually to identify opportunities for optimisation, thereby keeping waste to a minimum without compromising on quality.
PRODUCTION
Our main Völkl factory in Straubing is one of the world’s most advanced ski production plants. The German location and “Made in Germany” quality promise allow us to directly control working conditions, contribute to regional value chains and support the EU economy.
The energy management system at our factory in Straubing is certified according to DIN ISO 50001. In the interests of clean production, we have significantly reduced the use of poisonous and hazardous substances at Völkl, and we have completely eliminated them from many stages of production. For example, the hazardous substance dichloromethane (DCM) is no longer used in the production process.
The recirculation of grinding water has allowed us to reduce water consumption by almost 50%. Recycled materials, such as steel edges and coatings, generally play an important role. Up to 28% of our skis are now made from recycled or sustainably produced materials.
USE AND DISPOSAL
Völkl’s high-quality, long-lasting products are a key element of our efforts to be sustainable. This is complemented by a complaint processing and repair service in Straubing, which prevents the disposal of an entire product by replacing individual parts, thereby reducing the use of materials.
We work closely with certified regional waste disposal service providers and put great emphasis on the extensive reuse and recycling of individual materials including aluminium chips, steel, paper and wood.
DISTRIBUTION
Reusable, returnable packing is also used to distribute our products. Where cardboard packaging is required, we use sustainable products made of 75 percent recycled, FSC-certified paper from responsibly managed forests.