Stealth Launching A First To Market, Seam Welding Technology - Removes The Need For Stitching
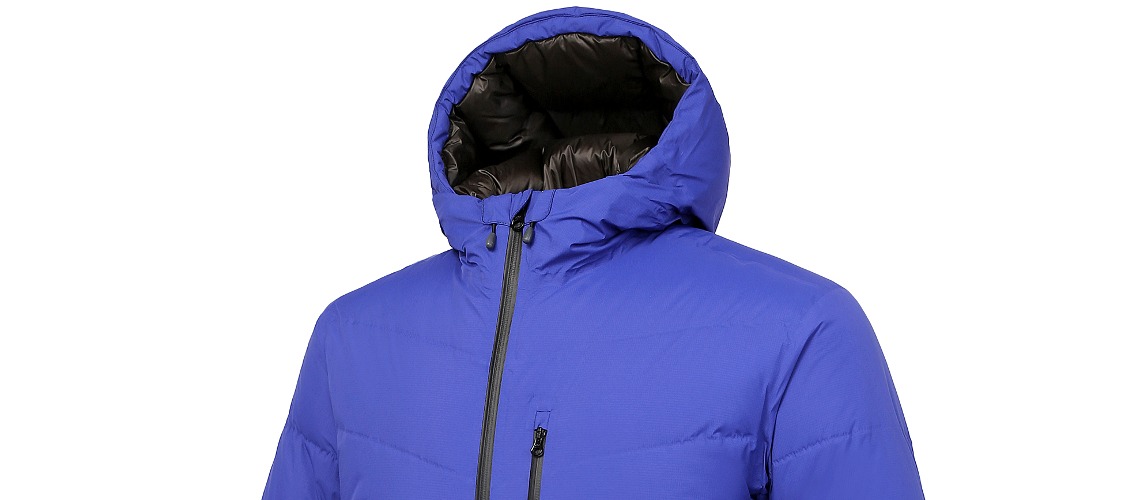
This April, Stealth, the leading global manufacturing experts in performance gear, is launching a first to market, patented seam welding technology that removes the need for stitching.
Stealth have developed and patented a novel method of welding seams that uses ultrasonic edge-joining combined with HF radio welding of a tape seal.
The technology results in seams that are tougher, warmer and entirely durable, for longer-lasting products that protect adventurers from the harshest elements. This expertly engineered welding process uses no stitching, no external heat and no glue, making performance wear: 50% stronger, 90% warmer, half the thickness of traditional seams*, and enables lightweight fabrics to be welded without damage for the first time in history.
Stealth’s revolutionary technology is masterminded by two manufacturing experts; Richard Strompf, also an outdoor adventurer and chemical engineer Karl Lu who share a common belief that outdoor and performance wear has a major problem – it’s stitched.
Despite the rapid evolution of performance fabrics over the last decade, many manufacturing technology processes that promise protection against the elements are failing through; weak seams allowing seeping water and air, weak glue that delaminates over time and heat damage through the application of tape.
Since the sewing machine was invented almost 200 years ago, there has been no significant robust alternative to seam construction – until now. Stealth uses a patented sonic and high-frequency process capable of welding a choice of synthetic based materials derived from virgin, recycled or bio (plant based) sources. Across apparel, outdoor gear and tents, Stealth’s new welded seam technology provides endless possibilities for performance brands to create game-changing performance products.
Karl Lu, the inventor of Stealth, says; ‘There’s too much outdoor gear today that fails after only a few seasons – we wanted to create performance products that last. We know that 80%** of the climate impact happens in manufacturing, so making durable gear that lasts longer is key in our sustainability efforts.’
Stealth provides a world of performance without compromise – tougher, warmer, entirely durable. No weak links, no doubts, no vulnerabilities. Now the world and nature can be experienced close-up without fear of your gear failing you – Stealth seams set you free!
Stealth revolutionary technology was born from the minds of Richard Strompf and Karl Lu, two manufacturing experts at the vanguard of their fields who shared a common manufacturing problem.
Richard, an outdoor adventurer, combines his first-hand experience facing the harshest of conditions upon the oceans and land with thirty years in performance gear production to form a unique understanding of how vital the durability of the performance of all-weather gear is. Karl, a chemical engineer and manufacturing expert, has a long history of innovation through developing new products and technologies and modernising process-driven production methods.
At a meeting in 2007 in Jangzhou, China, the pair realised they had a shared problem with lightweight performance gear. Traditional manufacturing methods meant lightweight fabrics of less than 100 deniers were problematic in production and led to quality issues; stitching weakened the seams, and the glue used to fix a water-proofing seamtape was prone to delamination. Alternative options using high-frequency welding also created problemsas the heat used to fuse the seam damaged the fabrics. The duo committed to overcoming the problem that faced them both.
Ten years ago, explorative trials began using pioneering sonic and high-frequency technologies; and in 2016, they formed Stealth welded seams. Through Richard’s and Karl’s persistent efforts, they had created for the first time a method to seam 100 denier and super lightweight fabrics without compromising the quality or performance of the products. Stealth had developed the world’s first and only sonic and high-frequency seaming method that uses no stitching, glue, and external heat.
In 2017 Stealth quickly began producing the world’s first lightweight air mattress before progressing to watertight bags and sleeping bags. Stealth now makes a full range of performance products, adding tents and apparel to their manufacturing capabilities in recent years. And with a new sustainable solar-powered factory due to begin production in the autumn of 2022, the possibilities of applying Stealth seaming technology are limitless.
To join the stitch-free revolution, please contact: Ben Mears info@stealthweldedseams.com / +44 79004 35199 – Limited manufacturing space for premium performance brands is being offered from Autumn 202