Salomon Annecy Design Center Pivots To Develop Face Masks
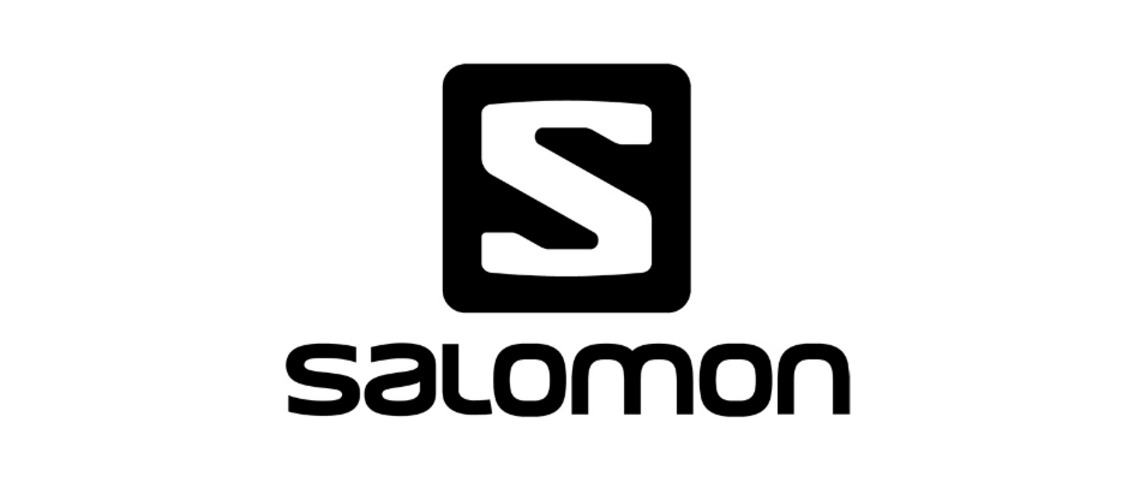
Today, Salomon, the four-season mountain brand, announces that it will shift from prototyping gear in its Annecy, France headquarters to developing reusable, non-medical grade face masks to fight the spread of COVID-19. The Annecy Design Center (ADC) is home to specialists in textile production who typically work with athletes to design prototypes of the latest in Salomon’s gear, footwear and apparel product ranges. Now, their decades of experience will go toward developing protective face masks that will be used to protect against the spread of COVID-19, with the goal of delivering 90,000 from April through June.
“There’s a lot of uncertainty in the world these days, and we’re all doing our best to make the most of tough situations and help with whatever means we have available to us,” says Becky Marcelliano, outdoor marketing manager at Salomon in North America. “Individually, we all understand that the best way to help is by staying home. As a company, we are trying to contribute with whatever means we have available to us, whether that means donating shoes to hospital staff here in the US and across France, partnering with our athletes to raise money or completely rewriting the script for our prototype lab to develop masks. Locally, we are also working daily on some other ways to help those in need until we’re safe, healthy and able to play outside again.”
They sit somewhat quietly, always at least two meters apart, in an expansive space inside Salomon’s Annecy Design Center (ADC) in the French Alps. There are 10 of them here, all are specialists in textile production with decades of combined experience. They are the people who staff Salomon’s Soft Goods Prototype Center, and normally these uniquely talented creators are building prototypes for Salomon’s future apparel and gear product range—footwear, jackets, ski boot liners, backpacks and more. Today, however, they are making protective face masks that will be used to protect the rest of us from the spread of COVID-19 in the weeks ahead. Their goal is to deliver 90,000 masks from April until June.
It’s a slightly different project than collaborating with a trail runner like Kilian Jornet, Francois D’haene or Courtney Dauwalter on a new pack or hydration solution or building a more comfortable liner for a Nordic ski boot. Indeed, the variety of outdoor products the group normally works on is mind-boggling. Now, they are focused on one product only.
Faced with the shortage of protective masks in the country, the French government launched a national appeal to the French textile industry. With the industrial tools in place to help, a French company called Chamatex proposed a solution—washable and reusable textile multilayer masks. The masks are certified by the DGA (Direction Général de l’Armement) and will be intended primarily for administrations and industrialists in all sectors of the business community in the near future.
As requests for the masks increased in recent days, Salomon got a call from Gilles Reguillon, CEO of Chamatex, because of the relationship between the companies and because Salomon has the ability to produce prototypes of all kinds. Within five days of the initial request, the team at Salomon was at their work stations at the ADC making masks.
“Chamatex is a French company that has been an industrial partner of Salomon’s for more than five years,” says Guillaume Meyzenq, Salomon’s VP of Footwear. “We have been using their ‘MATRYX’ technology on a number of our premium footwear models. They share the same passion for innovation that we do and they have unique talents for making innovative textiles.”
Despite being eager to help, the Salomon prototype center team was forced to stay at home like everyone else in France in recent weeks in order to comply with safety restrictions set in place by the government. Last week, however, Salomon got the call from Chamatex that their skills were in need.
“We like to say that, in a normal day, we might make a prototype shoe that helps Kilian Jornet go to the top of Everest in the morning and a sports bra for our running range in the afternoon,” says Jean-Noel Thevenoud, who manages the prototype lab. “So this is a different project for us, but the team has been eager to help since the crisis started. When we got the call last week, everyone was ready to go. We’ll get back to making outdoor sports gear soon enough, but right now we are very happy to use the skills of the team to help in these times.”